Newsroom
Activities That Benefit the Environment on a Global Scale
Automotive Systems is dedicated to achieving virtually zero CO 2 emissions by FY 2022 through energy conservation initiatives being undertaken by all employees, and by adopting renewable energy and operating with electricity derived from 100% renewable energy sources. However, these goals can not be accomplished overnight. They can only be achieved as the cumulative result of onsite initiatives at each of our business sites around the world. Here, we will introduce some of the environmental efforts underway our business sites.
Panasonic Automotive Systems Automotive Systems Business Division Shirakawa Factory Changing Environmental Awareness through Continuous Improvement Activities
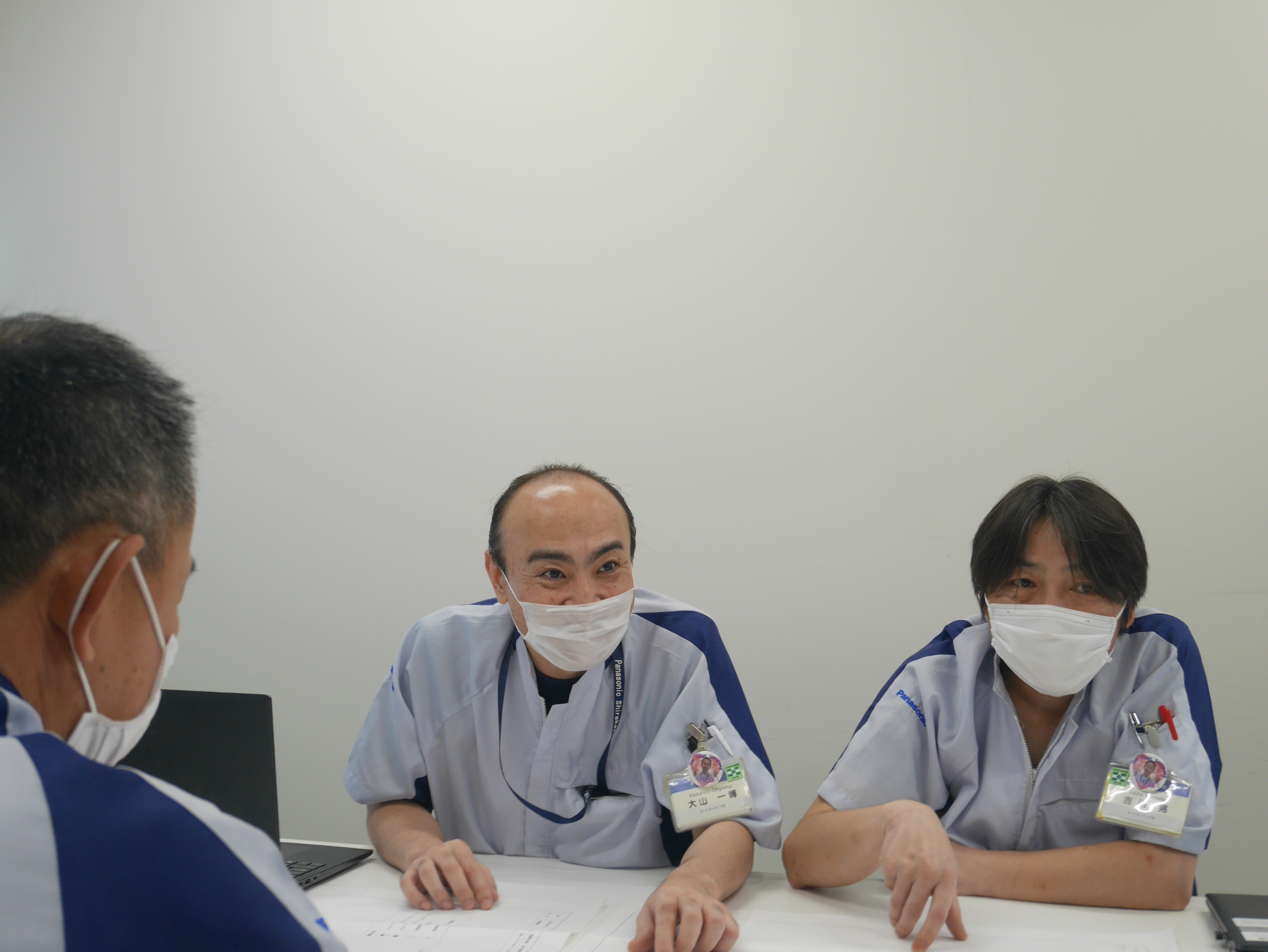
According to Mr. Oyama, the promotion leader, “The Shirakawa Factory, which began operation in 1974, has been continuously implementing energy-saving activities such as installing LED lighting, reducing cardboard use, and using returnable boxes. To be honest, it is a daunting task to achieve our target of 3% annual reduction in CO 2 emissions.” “All we can do is to find any waste, no matter how small, and work steadily to eliminate it.” With this in mind, we had a series of meetings with our members with the support of the Environmental Promotion Department in the beginning of 2021 when we began full-scale studies.
The Shirakawa Factory started out with technology for professional cameras, expanded into in-vehicle cameras, and now not only mass-produces finished cameras, but also ships core component sensor modules for in-vehicle cameras globally to factories in China and Mexico. We see room for improvement in the Shirakawa Factory clean room, which has an annual production capacity of 14 million units and operates 24 hours a day.
“The first thing we tackled was improving air leaks from equipment. There are more than 100 pieces of equipment in the clean room, and it all needs to be turned off to eliminate noise so that we can check for air leaks. This facility operates on a 24 hour schedule, so the only time we could do this was during the year-end holidays when operations are suspended. With the cooperation of the related staff, we identified and mapped all the air leakage points at once, and the repair work is still ongoing. This work is expected to save 12 MWh per year. Once this work is completed, it will also help lower the shared air pressure supplied to each line. We are also considering other ways to reduce power consumption by reducing the differential pressure between the clean room and other rooms. To this end, we are accumulating data to visualize how the time of day, environment, and other conditions cause fluctuations in the differential pressure.”
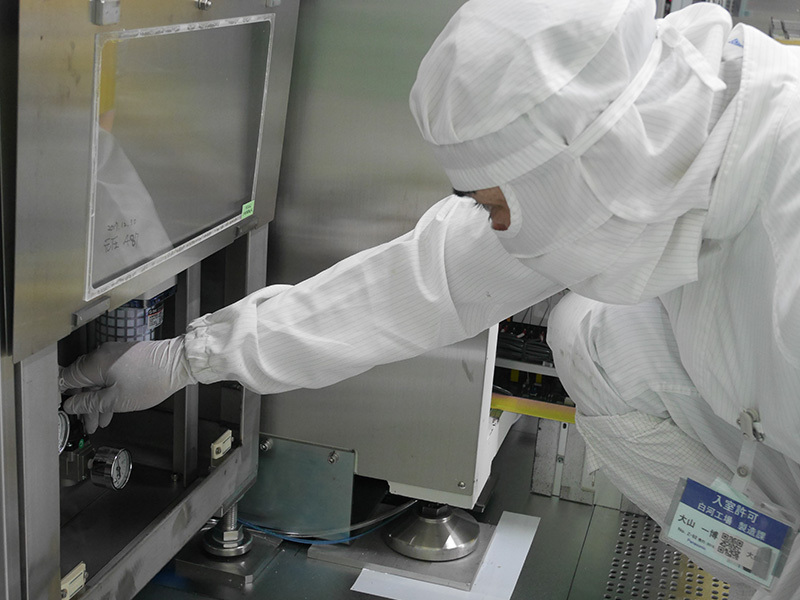
“To be honest, it sounded impossible at first. Now that we are gradually seeing results, I feel a sense of accomplishment and fulfillment. Through this experience, we learned the importance of continual steady efforts. But even more importantly, we need everyone at the factory to appreciate the importance of this kind of environmentally conscious effort. It is meaningless for a few people to work hard to improve facilities, if the improvements only revert over time. I hope to raise the awareness of all current members regarding the importance of steady effort, even if it is small.”
Panasonic AS Asia Pacific
Received the FY 2021 AM Company Environmental Award for the Introduction of Wi-Fi Switches for Air Conditioner Control
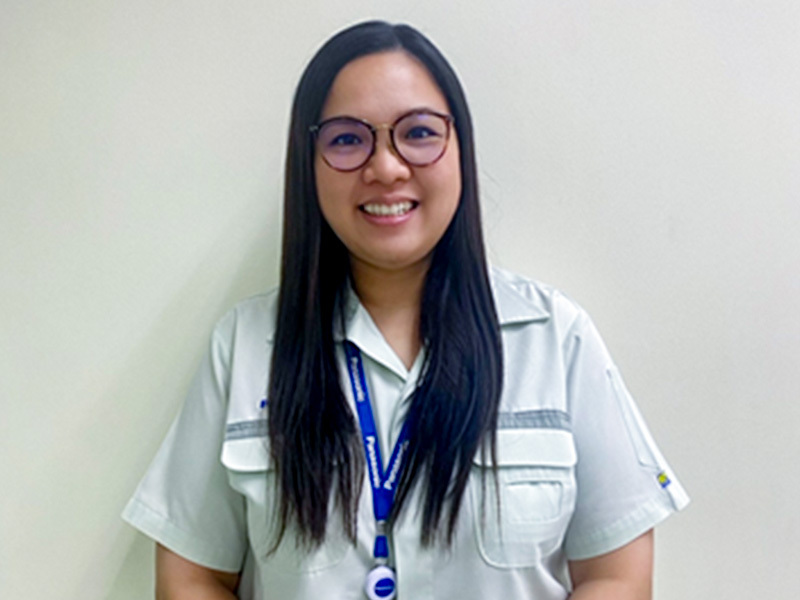
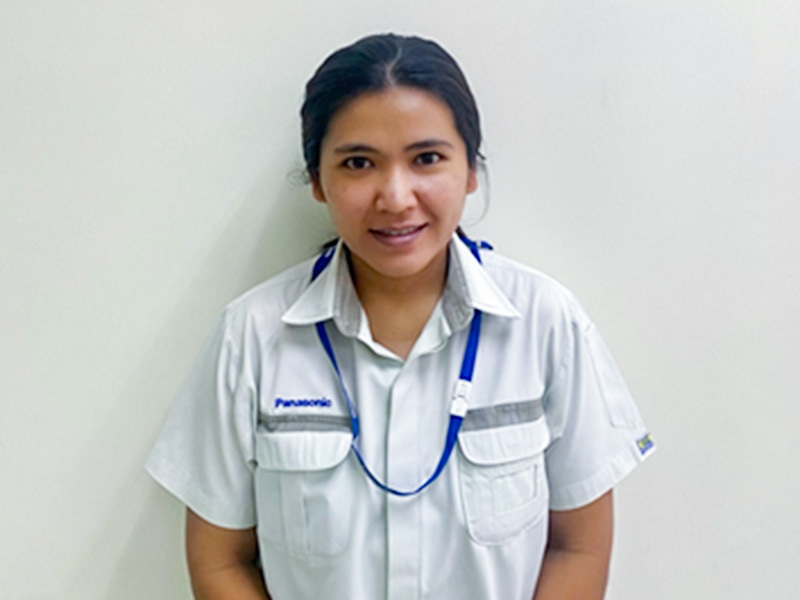
Ms. Kronrawee and Ms. Rarai have been with the company for 7 years. While conducting environmental efforts, their focus was on the power consumption of air conditioning. Approximately 40% of energy consumption in PASAP for 2019-2020 was due to air conditioning. The average temperature in Bangkok, Thailand, which has a relatively hot climate, is 30.6 degrees Celsius, similar to midsummer in Japan. Without air conditioning, long hours in a factory can have a negative impact on workers’ physical condition. After repeated discussions about reducing power consumption while maintaining the temperature, we decided to install a Wi-Fi switch to automatically maintain the temperature setting between 23 to 27 degrees Celsius.
The most difficult part was the installation of Wi-Fi switches for each unit, which required a power outage of about one hour, so the installation work had to be carried out on a non-operating weekend. Despite working on weekends, the active cooperation of the related members allowed us to successfully install all of the switches by the deadline. The result was a reduction of approximately 500 kWh electricity consumption and 256 tons of CO 2 emissions. “I am very happy that I was able to contribute to the company’s business activities,” said Ms. Kronrawee.
“As a result, we received the AM Environmental Award in FY 2021 and the Panasonic Group Manufacturing Award in FY 2022. I want to thank everyone who helped us.”
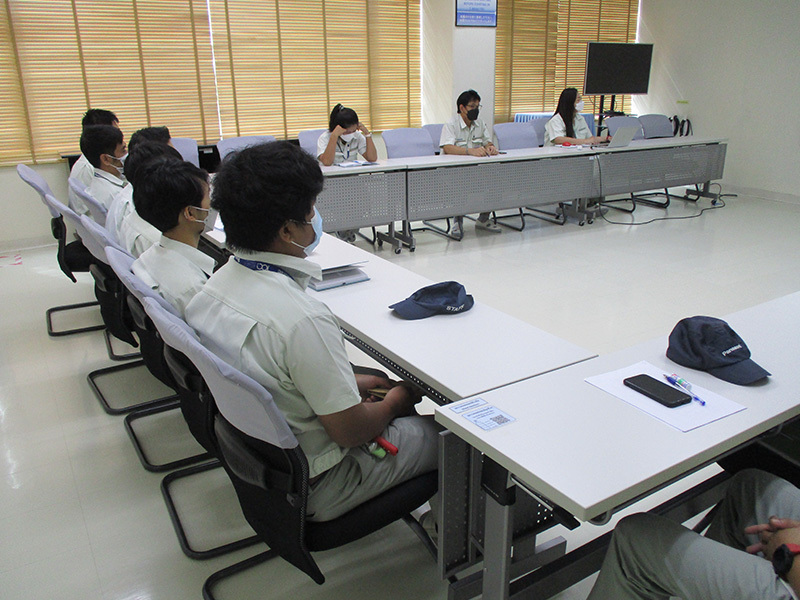
Panasonic Automotive Systems Headquarters (Yokohama Building)
Leading the Way with Locally Rooted PAS, Setting an Example for the Entire Panasonic Group
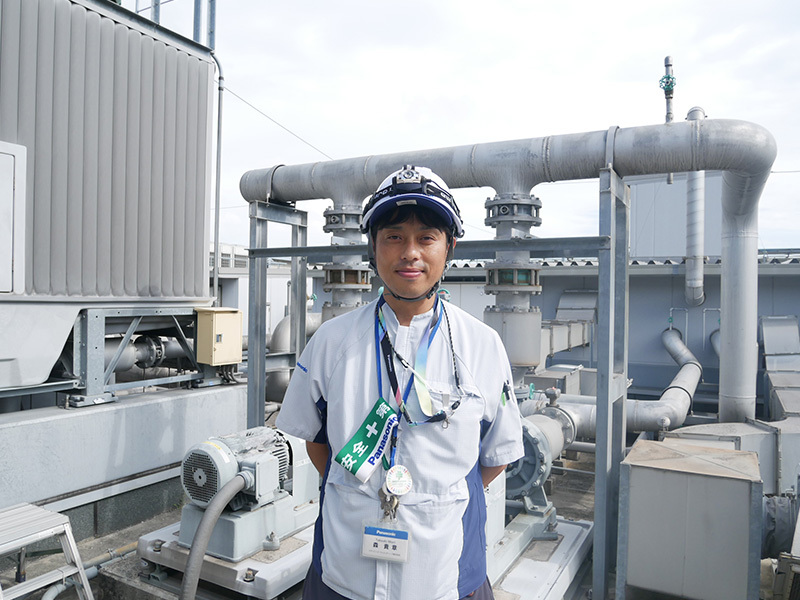
There is a high possibility of power shortages in the TEPCO service area, and we must fulfill our role as a company rooted in the local area by proactively responding to power conservation requests.
“Although the Yokohama area is a challenging environment, all of our sites are working on CO 2 reduction in various ways, both large and small. We all need to cooperate to make many small improvements,” says Mr. Mori of the General Affairs Department. Most recently, we have been working on the formulation and implementation of rules for power-saving measures in the event of a warning or alert for power shortages.
“CO 2 reduction activities have been ongoing since 2008, when the headquarters (Yokohama Building) was founded. As of 2016, when I arrived, the building was young and the facilities were relatively well maintained. Areas that contribute greatly to CO 2 reduction, such as the application of heat shield film and updating to high-efficiency type equipment, have already been implemented, and every year I am painfully aware that it is not an easy task to achieve the 3% annual target (laughs).We have also been upgrading our cold water supply pumps, outside air conditioners, and exhaust fans with inverters. However, we need to adjust the settings on a daily basis to optimize the intake and exhaust air balance in accordance with the ever-changing environment, such as seasonal changes, long holidays, and the COVID-19 pandemic. Even now, we visit the site to adjust to the optimum conditions, and there is no end to this effort. However, this work has allowed us to find subtle room for improvement, so I recognize the importance of this continuous effort. Since our core business is manufacturing, we cannot afford to interfere with development research and its operations. We need to maintain an efficient work environment while also reducing CO 2 emissions.”
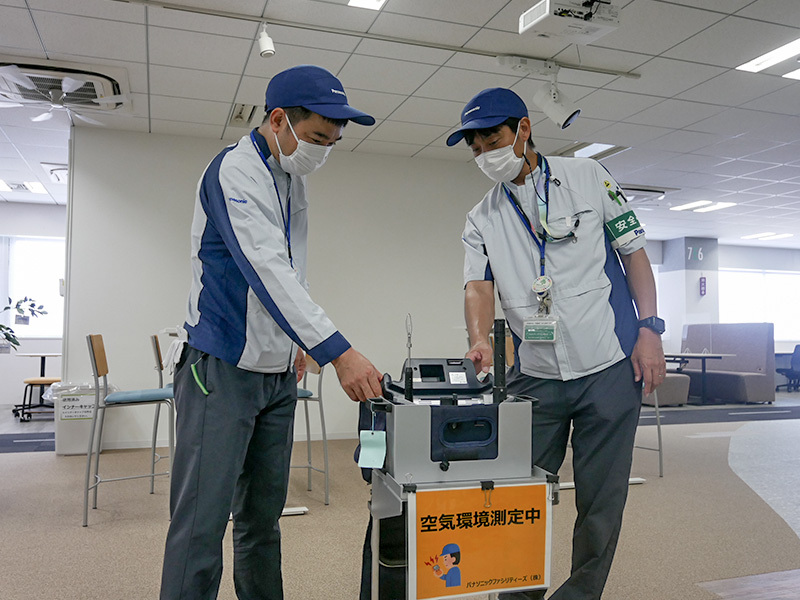
Currently, the company is reviewing the possibility of a reduction of approximately 5 million yen per year by updating the excess exhaust fans toward 2023, so this will be a steady result.
“Car manufacturers are major customers for the products we manufacture, and we cannot continue our corporate activities together with our customers who are proactive in addressing environmental concerns unless we constantly improve and grow together. To live up to the name of Panasonic Automotive Systems, we will continue to take the lead at the headquarters (Yokohama Building) and set an example for Panasonic as a whole.”