Newsroom
Excellent Skills Accelerate DX at Tsuruga Plant
Tsuruga Plant
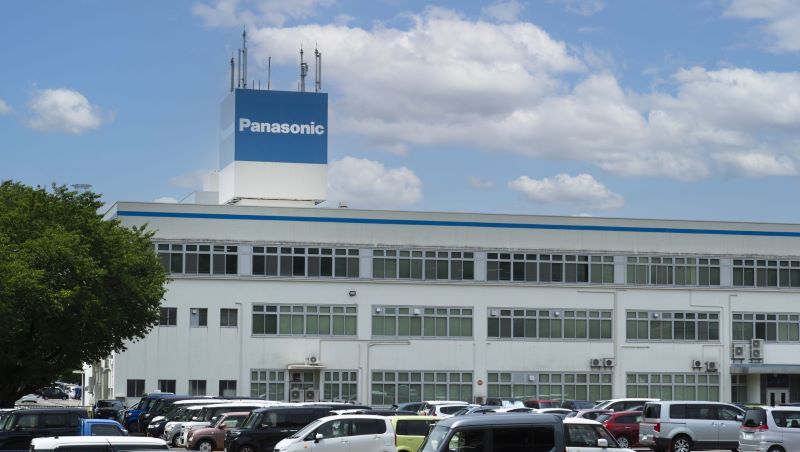
Development and manufacturing staff work closely under one roof at Tsuruga Plant. Excellent manufacturing skills are passed down from veterans to young employees.
The Tsuruga Plant is located about a 15-minute drive west of JR Tsuruga Station in Fukui Prefecture. The plant started operations in 1974 and produces in-vehicle switches, such as combination switches, steering wheel switches, and instrument panel switches, as well as sensors, including steering angle sensors and back and corner sensors, and in recent years, head-up displays have been added to their lineup. As the world’s leading kaizen factory, it leads global production in Thailand, Mexico, and China.
Its strength lies in the teamwork of development and manufacturing staff who work closely together under one roof. When a request for quotation(RFQ) is issued with a car manufacturer’s requirements for a product, including specifications, functions, cost, production volume, and design, to our design department, the manufacturing department also starts discussing the production method. The employees in charge of product development, equipment development, and manufacturing processes constantly work together to make and revise improvement proposals so that they can meet customer expectations. This approach has fostered a culture of thorough commitment to the quality of in-vehicle products.
The manufacturing site uses the latest digital technologies to visualize waste and stagnation by using AI to analyze videos captured by 360-degree cameras, and makes daily improvements based on individual suggestions and ideas. Since fiscal 2018, we have been working to improve our manufacturing site quality and efficiency using the Toyota Production System (TPS), and operations that combine TPS with DX are now further upgrading the production site. It has become the site where the Panasonic Group implements cutting-edge manufacturing practices.
The key to staying on the cutting-edge of manufacturing practices lies in the development of technicians who can take the lead at the manufacturing site. We hold the Manufacturing Competition every year with the aim of improving and developing the skills of manufacturing personnel. Each year, the winners of the in-house qualifying round compete at the Panasonic Group Competition held in October.
This section introduces a mentor who strives to train junior technicians beyond the boundaries of the base and a young technician who has lived up to his expectations.
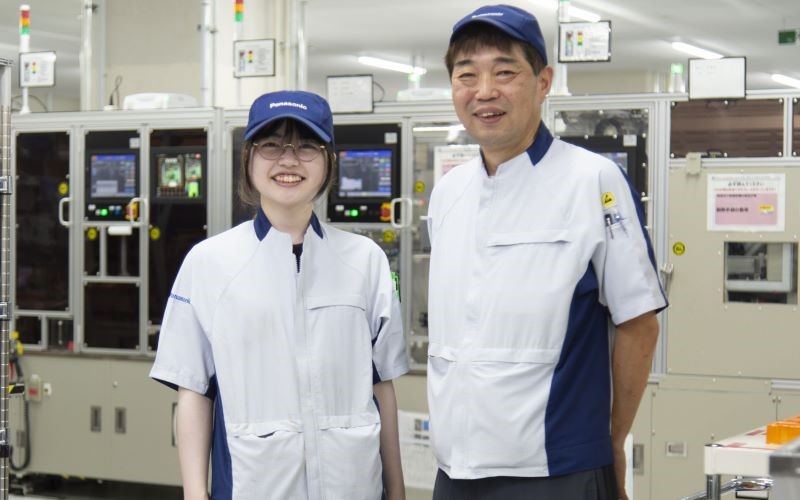
Mr. Teruhiko Morishita (right):Joined the company in 1983. He is in charge of equipment maintenance and management including troubleshooting production lines and management of spare parts required for repairs. He has a certificate of the Panasonic Group’s 1st grade Certified Skilled Worker and is active as a committee member in charge of the management and operation of competitions. His high-level skills are appreciated and in demand, and he responds to requests for guidance not only from his own division but also from other workplaces.
Ms. Sachie Mizuguchi (left):oined the company in 2022. In the Production Engineering Department for back and corner sensors, she works on improvements in productivity by visualizing site production status and data. In the competition, she is taking on the challenge of the mechanical complex competition in which participants process, assemble, and wire parts within the given time and compete on the accuracy of the finish.
Q: What type of mentor is Mr. Morishita?
Mizuguchi: Without Mr. Morishita’s guidance, I couldn’t have participated in the mechanical complex A-rank competition. When I face a hurdle and ask him what to do, Mr. Morishita works with me through trial and error to find the way that works best for me. Thanks to Mr. Morishita’s accurate advice, I gradually become able to complete each assignment.
Morishita: I just teach the basics of work in manufacturing and not a special method. Show them how to do things, let them try it, and then modify it to suit them if it doesn’t work for them. This is the flow of my mentoring practice. I have been mentoring new employees for more than ten years.
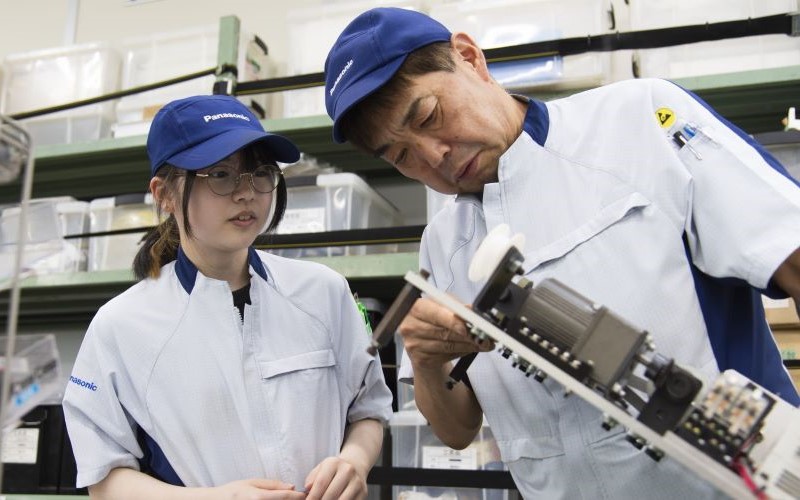
Q: Mr. Morishita, you are working beyond the boundaries of the organization to train and develop technicians.
Morishita: I will be retiring next year. I want to train as many technicians as possible. That’s why I give guidance to those who ask me for training, regardless of which organization they belong to. What I aim to do during training is to bring every trainee to the same level. This will eventually raise the level of the entire production site.
When I was young, there were no technical instructors, so I had no choice but to learn by watching my senior colleagues do their work. It is very difficult to raise the level of your skills on your own without a mentor. I have continued to learn by asking other bases for guidance and trying the methods of competition participants from other domestic and overseas bases. I would like to still continue to learn and solve problems at our site with new manufacturing methods.
Q: What is your future goal?
Mizuguchi: This is my third year in the company. I feel that I will be taking more of a lead in my work. Mr. Morishita’s guidance is on how to prepare for mechanical skills combined competition, but there are many things that I can make use of in my work. I would like to master the skills and know-how that I have learned from him to grow as a technician.
Morishita: In recent years, there have been rapid changes in the manufacturing world, where DX is moving ahead. Along with these changes, manufacturing itself is changing. Production process no longer requires hand finishing, everything is mechanized. Still, without the hand finishing know-how, you can’t achieve successful DX. The skills to make things by hand will remain important in manufacturing in the future, and that is why I want to teach manufacturing skills to as many juniors as possible.
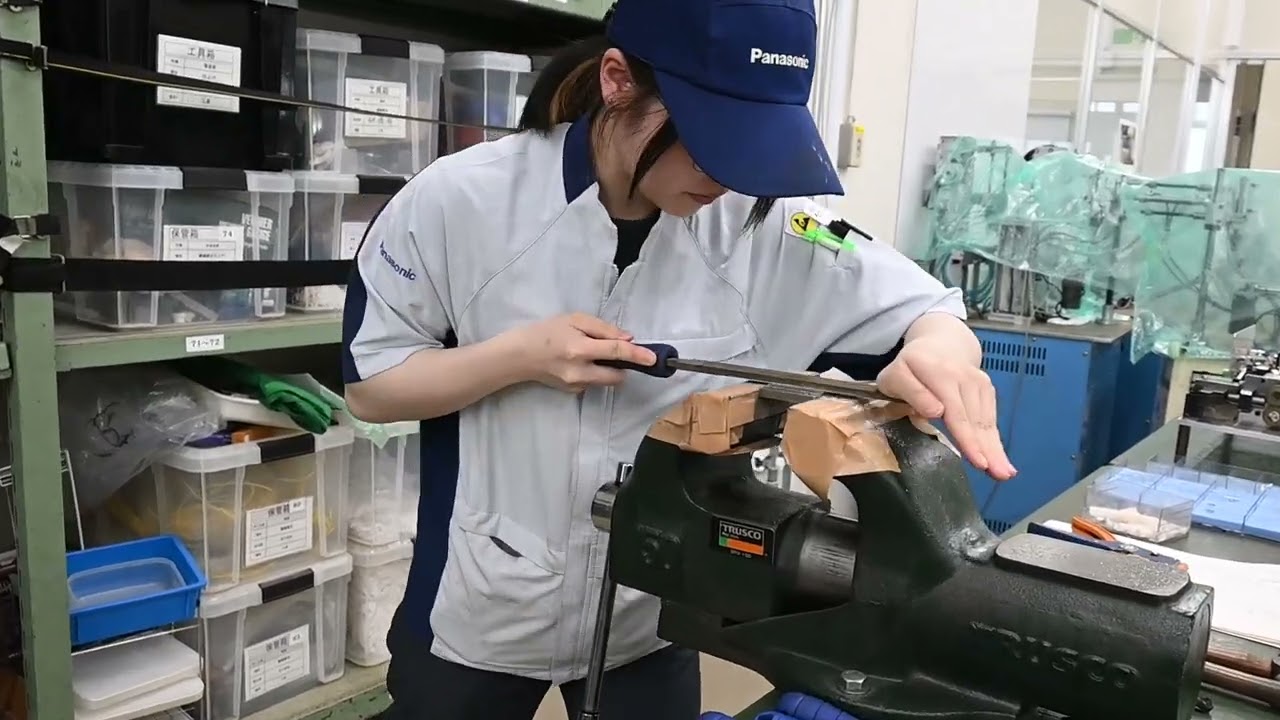