Newsroom
Masters of Operational Frontline Support: Ultra-high-mix, Low-volume Production Matsumoto Plant
Matsumoto Plant
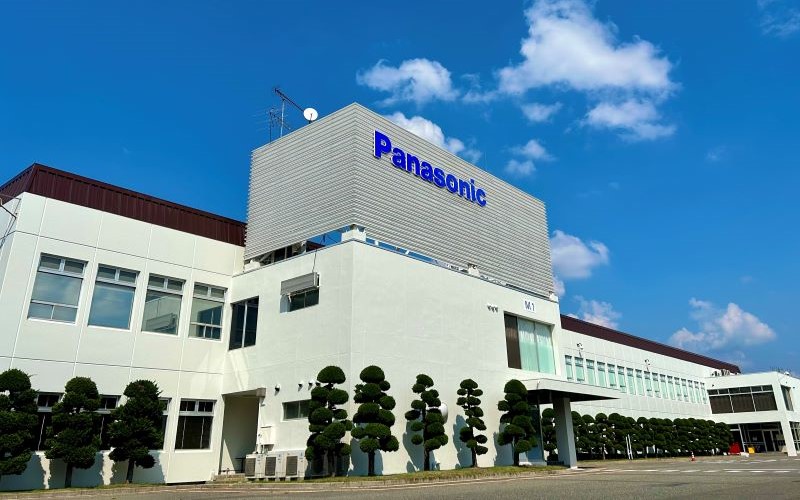
The strength of Matsumoto Plant lies in its ability to facilitate ultra-high-mix, low-volume production of more than 500 different models per product. The automotive industry is continuously undergoing major upheavals. We can survive these changes thanks to our responsive manufacturing capabilities.
Located roughly in the center of Nagano, Matsumoto is surrounded by the Japan Alps and rich in natural beauty. Traditionally, the area was known for production of watches and precision instruments. Our Matsumoto Plant is situated in the Okubo Factory Park Complex, about 20 minutes by car from JR Matsumoto Station.
The plant started operations in 1974, with calculators as its first product. The following year, production of car audio systems began, and it has led the production of in-vehicle equipment in the Panasonic Group from that day forward. Currently, in addition to manufacturing cutting-edge in-vehicle products that create comfortable cabin spaces, such as IVI (In-Vehicle Infotainment), display audio, and car navigation systems, the plant develops new manufacturing methods and trains the next generation of manufacturing leaders.
The strength of Matsumoto Plant lies in its ability to facilitate ultra-high-mix, low-volume production. For example, when manufacturing the IVI systems for car manufacturers, the plant produces more than 500 different products per series. Taking advantage of this strength in facilitating ultra-high-mix, low-volume production, we aim to be the number one innovator in the manufacturing industry.
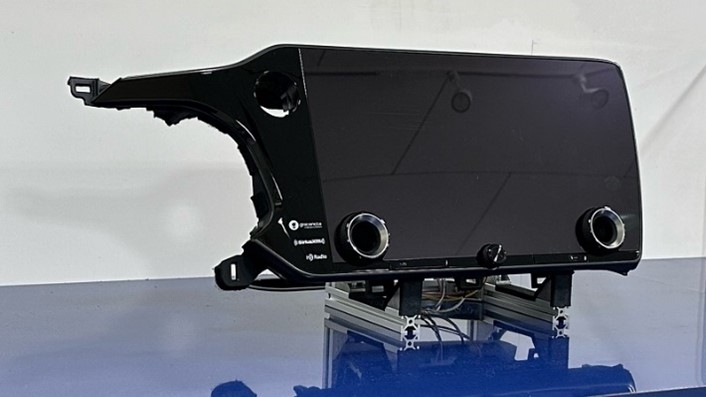
The ongoing drastic changes in the automotive industry make it essential that we are agile enough to respond to the increasing complexity and speed of software development for infotainment systems, which plays a central role in the manufacturing of SDVs (Software-Defined Vehicles). At the same time, the shortages in semiconductors and other devices in recent years have run up inventories. Domestic plants are facing a variety of other issues as well, such as soaring raw material prices due to the depreciation of the yen. One core approach we are taking to solve these issues is upskilling the technicians who play important roles at production sites where actual manufacturing activities take place.
We hold the Manufacturing Competition every year with the aim of improving and developing the skills of manufacturing personnel. Each year, the winner of the in-house qualifying round competes at the Panasonic Group Competition held in October.
Let’s meet our employees who exert themselves every day with the aim of winning the first prize (gold medal) in the mechatronics category, together with their comments.
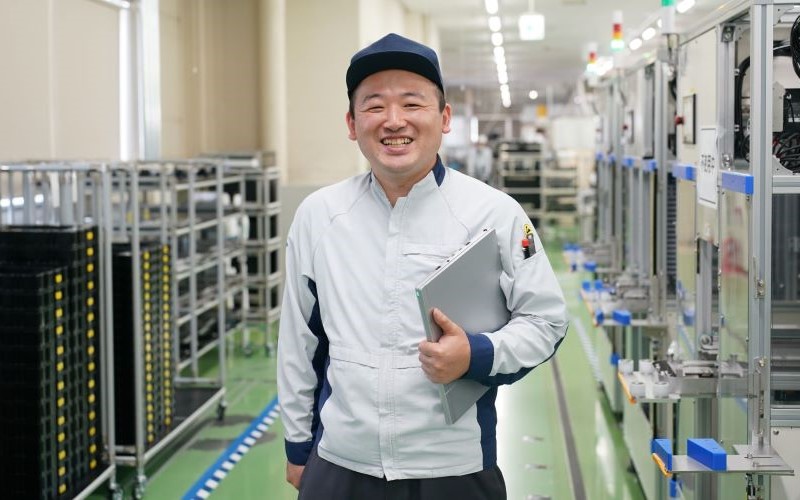
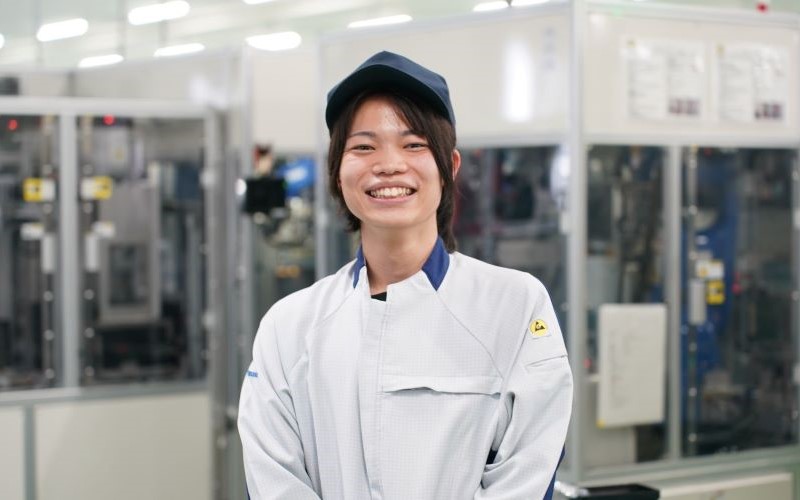
Q: What did you learn through participation in the skills competition?
Fujikawa: The biggest lesson I learned is how important preparation is. In mechatronics competitions, you are given time to check the equipment in advance, and it is fair to say that the results are determined by how perfect you can make the equipment conditions during that time. Preparing well in advance is that important, and the same holds true in daily work. It helps us efficiently carry out our tasks.
Q: How do you find Mr. Kobayashi's guidance?
Fujikawa: It is easy to understand. Of course, Mr. Kobayashi's approach does not always apply directly to me, so I try to adapt it to suit me and incorporate it into my practice. My day-to-day work is not at all related to mechatronics competitions, so weekly training is essential not to lose my touch.
Kobayashi: While I gear up for the competition about three months before it takes place, Mr. Fujikawa starts his preparation earlier. My coaching includes preparing practice problems at his request, providing him with the problems from previous competitions, and checking answers together. That was our approach this year as well. Since we have already prepared the equipment that was missing in the competition last year, I have no doubt that he will win the gold medal this year.
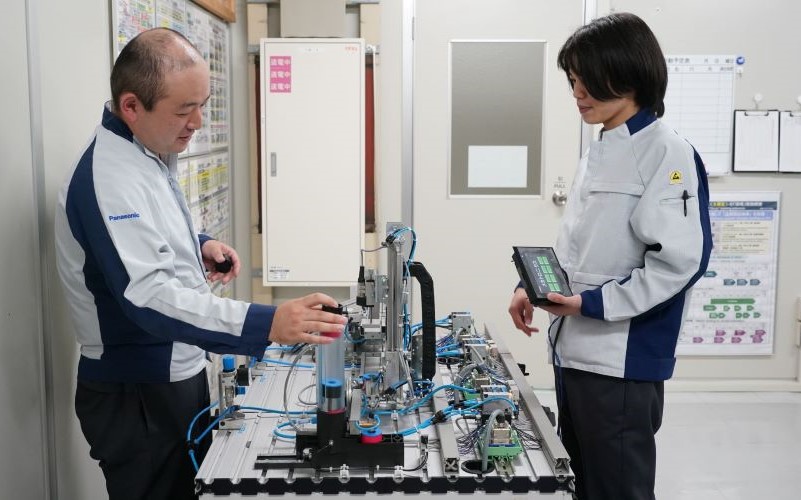
Q: What do you think is needed for manufacturing in these times of drastic changes that the automotive industry is facing?
Kobayashi: I am also experiencing significant changes on the manufacturing site. In order to adapt to the changes of the times, I think we need to keep up with each change one by one, continue to think about what we should do in manufacturing activities, and put it into practice.
Q: To make that happen, personnel development seems very important.
Kobayashi: Exactly. Showing them how to do things, letting them do them, and following up on the results. This flow is crucial for the development of manufacturing personnel. The senior who mentored me thoroughly focused on letting me try myself. Now that I'm in a position to mentor my junior colleagues, I am aware that it requires courage and commitment to entrust important work to others. I am grateful to my mentor for his approach, which he adopted with the belief that he would take responsibility if I failed. We cannot assign tasks to junior colleagues if we are always afraid of their mistakes. I hope to continue following his way of mentoring with courage.
Q: What are your goals for the future?
Fujikawa: Winning a second consecutive gold medal in the competition. Eventually, I would like to win a special skill award. I am aware that all I have to do to achieve this goal is work hard on daily practice with my performance on the actual competition stage in mind. I want to compensate for what I currently lack and solve as many mock problems as possible, and then do my best to take on this challenge.
I also would like to take up work that lets me leverage my knowledge and skills in maintenance and sequence programming to eventually make a contribution to the company. To this end, I will work on further improving my skills and grow to be a leader on the manufacturing front.
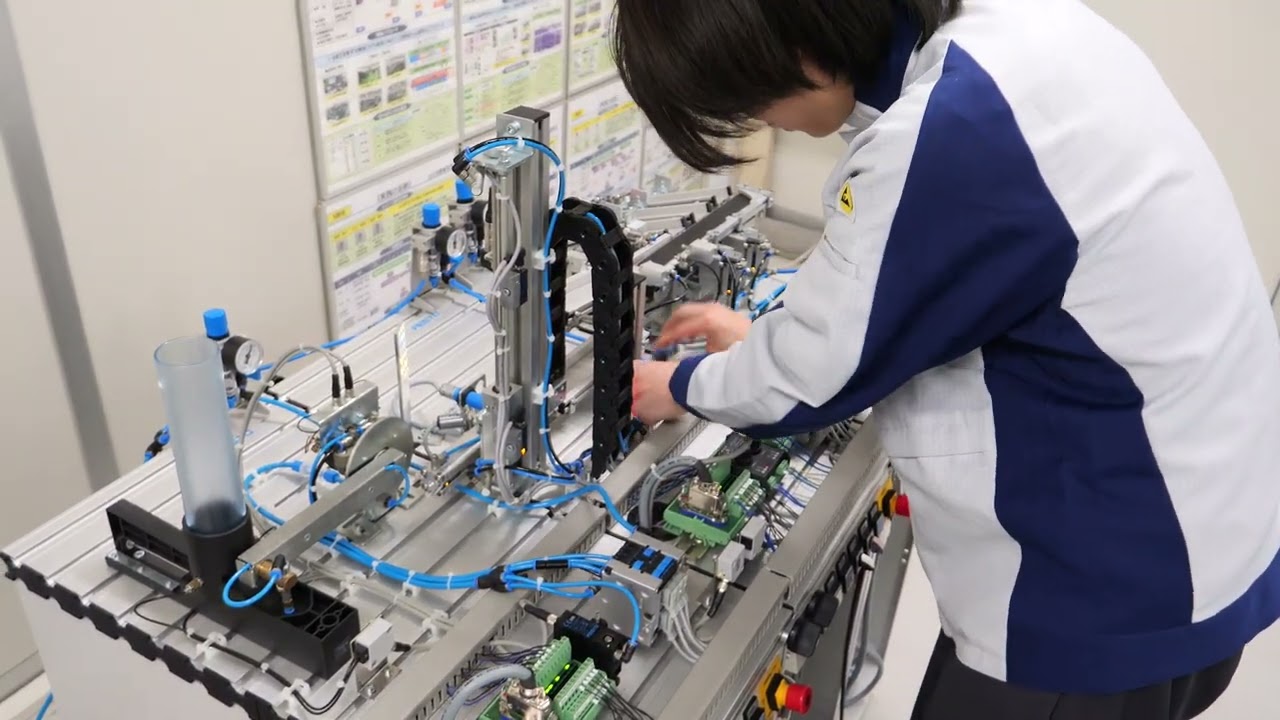