Personal and Professional Growth of Young Personnel Drives Manufacturing Evolution
Shirakawa Plant
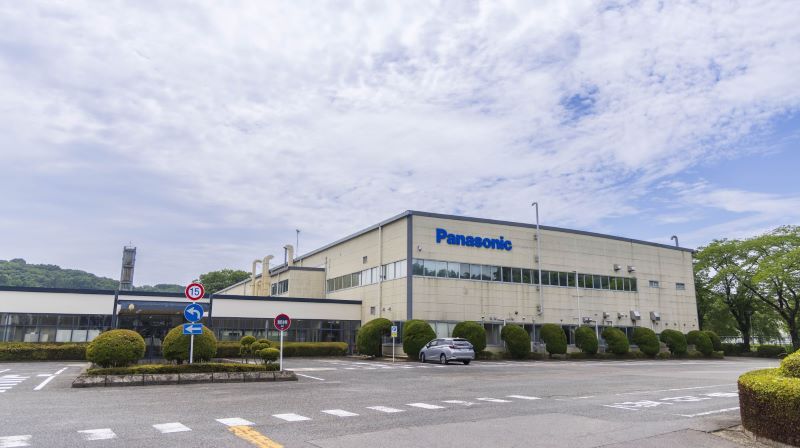
As a global core base for in-vehicle cameras, image sensor modules, and ETC in-vehicle equipment, the Shirakawa Plant takes the lead in manufacturing collaborations with plants in China and Mexico. We interviewed a young employee who is aiming for growth by passing on technology.
The Shirakawa plant is about 10 minutes by car from Shin-Shirakawa Station on the Tohoku Shinkansen. As a global core base for in-vehicle cameras, image sensor modules, and ETC in-vehicle equipment, the Shirakawa Plant is taking on the challenge of manufacturing high-quality, cost-effective products using cutting-edge product development technologies and new manufacturing methods in collaboration with bases in China and Mexico.
The plant started operations in 1974. Since its initial manufacturing of portable video cameras in 1982, the plant has produced a variety of video and camera products. Production of in-vehicle camera, our current main product, began in 1996. Since then, we have been working hard to expand and improve the functionality of in-vehicle cameras so that they can be used for sensing and vehicle control applications.
Cameras are optical products, and manufacturing greatly affects the quality of the product. For example, in the latest in-vehicle camera manufacturing process, high-level manufacturing technologies such as lens axis adjustment play an important role. Based on feedback from the manufacturing floor, the development division constantly review each design to find improvements for better manufacturing processes. By manufacturing higher-quality, lower-cost products, the plant enhances the functionality of safe driving systems that reduce the number of traffic accidents and the mental and physical burden of drivers, helping to create a safer and more secure mobility society.
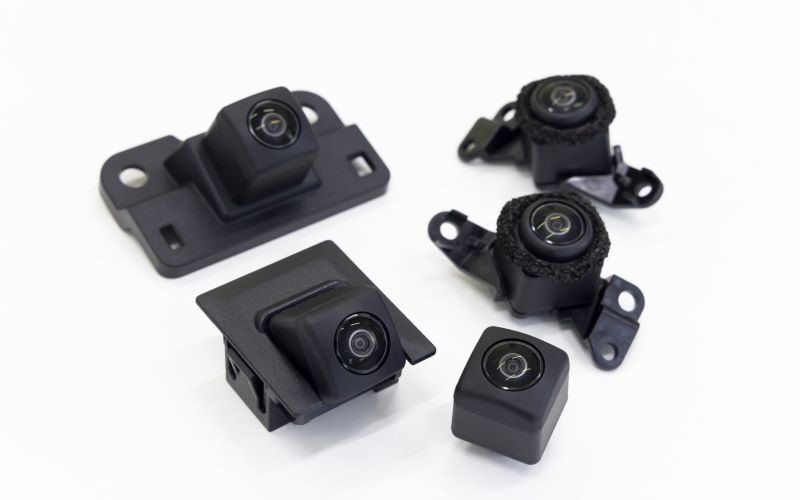
To rapidly solve manufacturing issues on a fundamental level, the Shirakawa Plant holds daily morning meetings where the supervisors of each function come together to exchange opinions and ideas and implement improvements. The plant also pays particular attention to ensuring psychological safety. The philosophy of creating work environments where “anyone can speak up without hesitation” has been put into practice across every aspect of the plant. By improving the workplace culture, each employee at the Shirakawa Plant is empowered to think about issues and solutions and is working as one to create the world's highest quality products.
One of the initiatives to develop personnel in the manufacturing division is to take on the challenge of the skills competition that draws participants from across the Panasonic Group. On the competition stage, employees from different backgrounds compete with the skills developed by training their minds and bodies. These skills then lead to improvements in their day-to-day work performance.
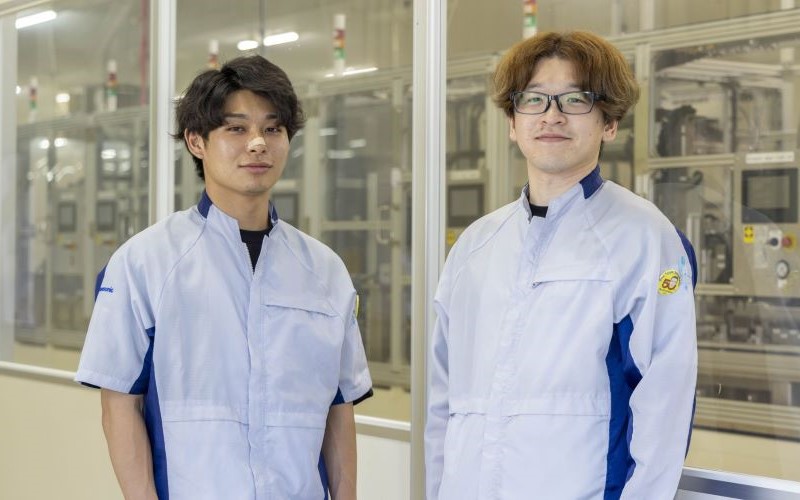
Mr. Yuma Kawasaki (right): Joined the company in 2018. He is in charge of process design for in-vehicle cameras, defect analysis, and loss reduction at global bases. Mr. Kawasaki is taking on the challenge of the electronics skills combined competition that tests skills in three processes: assembly, wiring, and programming. Participants compete to see who can complete items faster and neater.
Mr. Imaru Hitomi (left): Joined the company in 2017. He is in charge of the development, introduction, and maintenance of in-vehicle camera production equipment. Although there is only a one-year difference in age between them, he is coaching Mr. Kawasaki in preparation for the competition.
Q: What kind of guidance do you give to Mr. Kawasaki?
Hitomi: I have no more guidance to give about the basics. I instruct him on how to deal with problems on the day of the competition and how to find issues.
Kawasaki: He’s close to me in age, and it’s easy for me to talk to him and ask about any topic.
Q: What did you discover through your participation in the competition?
Kawasaki: I think that I am able to make use of the experience with the preparation and setup, which I gained through participation in competitions, in my daily work since we compete for speed. On the other hand, I feel that it is difficult for young employees to find time to address self-development, including participation in competitions. To drastically enhance manufacturing capabilities, I think we need to give consideration to how to organize and promote these kinds of activities and change the system to work on them as a company.
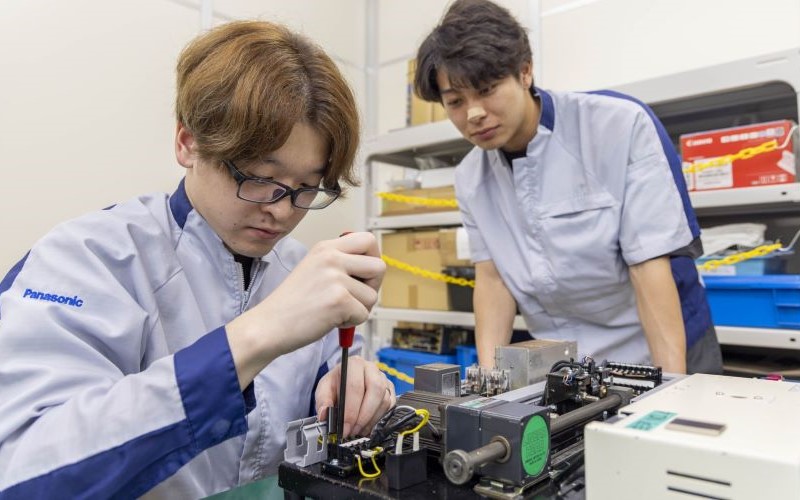
Q: The development of manufacturing personnel is also a company-wide issue.
Hitomi: We see this across our domestic bases, but there are very few intermediate-level employees to connect veterans and younger employees, which hinders the transfer of skills. This lack is caused by variations in the number of hires each fiscal year.
Skills can only be transferred by seniors actually showing how the work is done while giving guidance. However, much younger employees may hesitate to seek guidance from senior employees. I’m the oldest among the younger employees, so I’m trying to bridge the communication gap between veterans and younger employees. I have learned a lot from many senior employees, and now I feel that this is my role as a mentor.
Kawasaki: Improving communication is also essential for the development of manufacturing on a global scale. We produce in-vehicle cameras at three global bases, but different countries have different languages and customs. And we can see these differences in manufacturing. Even with the increasing automation of production lines, people will always be involved. For instance, during a business trip to Mexico last summer, I had trouble with communication gaps. When we deploy equipment and transfer work processes developed in Japan to overseas plants, we pass on a variety of know-how to local members, but it is often not communicated well. As with any job, it is very important to have good communication in order to bridge the gaps created by differences in the environment and ways of thinking.
Q: What are your goals for the future?
Kawasaki: With the help of my seniors and the company, I would like to create an environment where young employees can learn more. If you are swamped with your daily work, you have no time to think and can’t spare time for personal growth. However, if you don’t actively display motivation and eagerness, the people around you won’t feel the need to offer cooperation and help. That’s why I think, as future senior employees, it’s our responsibility to show that we’re willing to learn.
Hitomi: To meet the growing demand in overseas markets with our manufacturing capabilities, we need to further advance unmanned operations and automation at global manufacturing sites. I would like to evolve our manufacturing by developing more advanced manufacturing methods at sites in Japan so we can provide better products at lower prices.
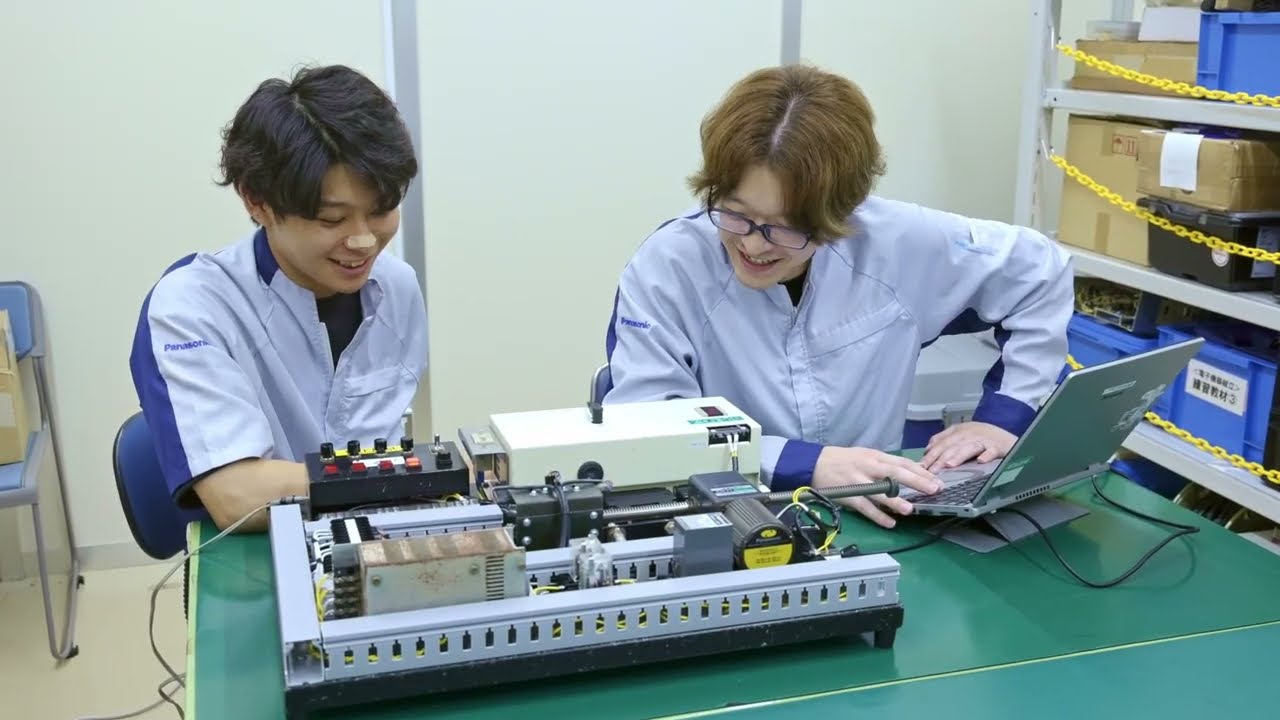