Gemba Innovation Dramatically Improves Management Power
Panasonic Automotive Systems Co., Ltd. in Tsuruga is promoting the Panasonic Group company-wide project, Gemba (operational frontlines) Innovation, ahead of other manufacturing sites.
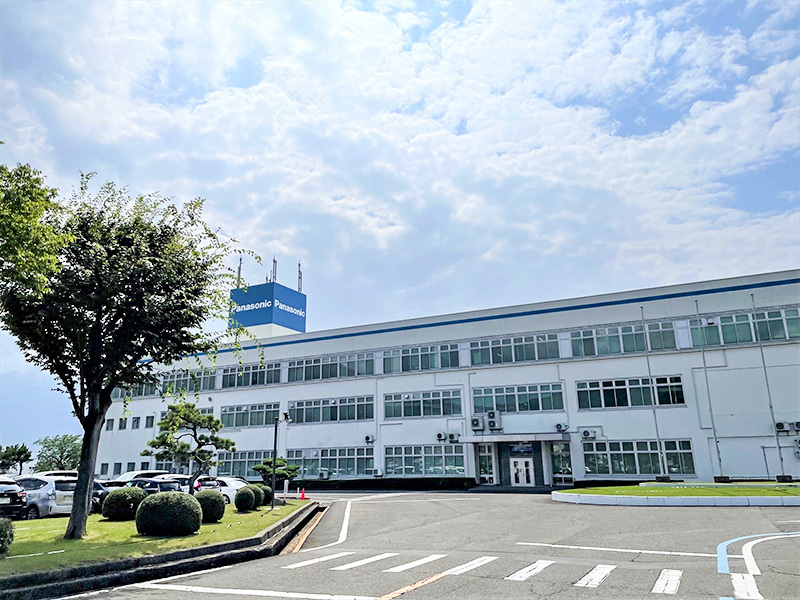
What is Gemba (operational frontlines) Innovation?
Gemba Innovation is an initiative to strengthen on-site operation capabilities by eliminating waste and stagnation from all sites, including manufacturing sites and logistics warehouses, and by streamlining the entire supply chain. The Electromechanical Devices Business Unit (BU), which has been involved in the development, manufacturing, and sales of in-vehicle parts for more than 50 years, has expansive know-how regarding eliminating waste and stagnation, and its employees have a mindset of making daily improvements (kaizen) at their workplaces. By adding the capabilities of digital technology to this site, we can expose further waste and stagnation that could not be identified by human capabilities and dramatically improve productivity.
Mr. Minamio of Panasonic Holdings, the leader of company-wide projects, is also the Executive Officer in charge of manufacturing at Panasonic Automotive Systems Co., Ltd.
“How can we eliminate waste? Always keep this in mind. In other words, it is important to enhance our awareness at the thinking process level. This awareness will ensure that we always have lofty goals,” says Mr. Minamio. Continuous kaizen, relentless kaizen, is the goal of Gemba Innovation. “When Panasonic’s diversity connects horizontally, it turns into value. The aim of Gemba Innovation is to lead this movement. We create greater value by connecting to the group from the manufacturing site,” he explains.
The specific activities of Gemba Innovation leverage the capabilities of each Panasonic Group company. For example, AI technologies from Panasonic Connect Corporation are applied to analyze on-site work, which used to take a great deal of time and effort, significantly reducing analysis time and labor. In addition, mutual visits between operating companies are also very active, and evangelists working on the ideology of Gemba Innovation at each site are putting the insights gained at other sites into practice to further develop and evolve the activities of their own divisions.
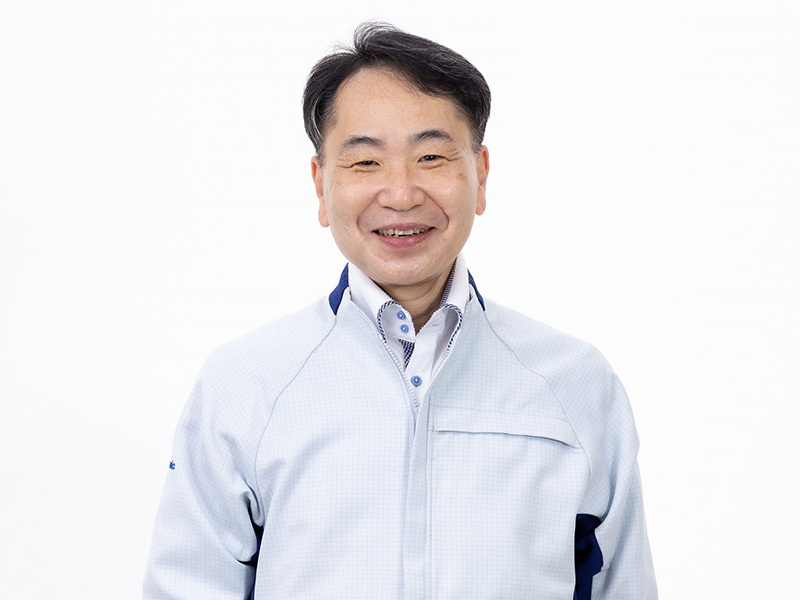
Panasonic Holdings Corporation and Executive Officer of Panasonic Automotive Systems Co., Ltd.
Productivity Doubled
Evangelists have been trained and are now active at sites around the world, with the mission of Gemba Innovation taking root at their worksites. Mr. Takeuchi, who is working as an evangelist at Tsuruga, explains how he approaches his activities. “I meet with the site team leader every morning, and I try to respect their sentiments.”
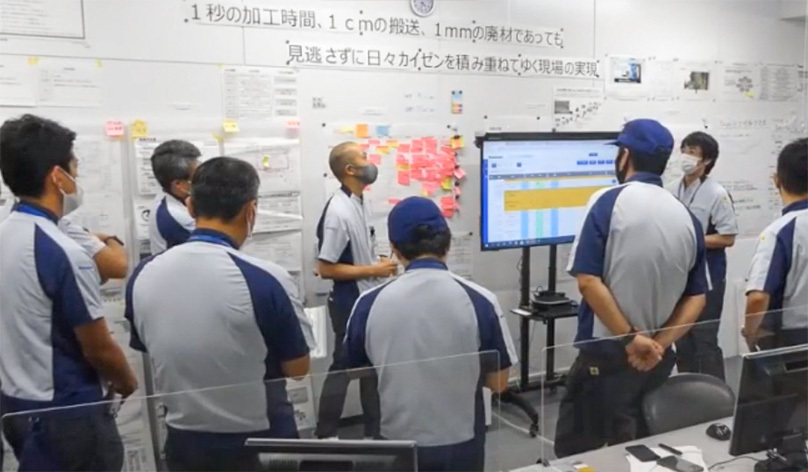
BU manager, and plant manager, meet to share information and review issues.
At the Electromechanical Devices BU, which develops, manufactures, and sells car switches and sensors, kaizen has taken root as a thinking process through longstanding relationships with car manufacturers. At the start of its Gemba Innovation activities, the company installed 360-degree cameras on part mounting lines and in the assembly process of steering angle sensors and steering ECUs to capture workers’ movements 24 hours a day, 365 days a year, using AI data analysis to improve on-site work efficiency.
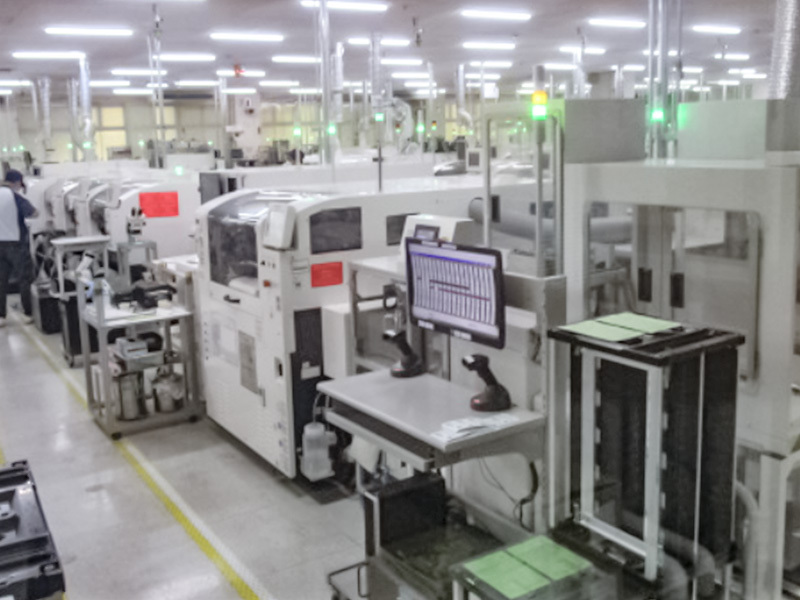
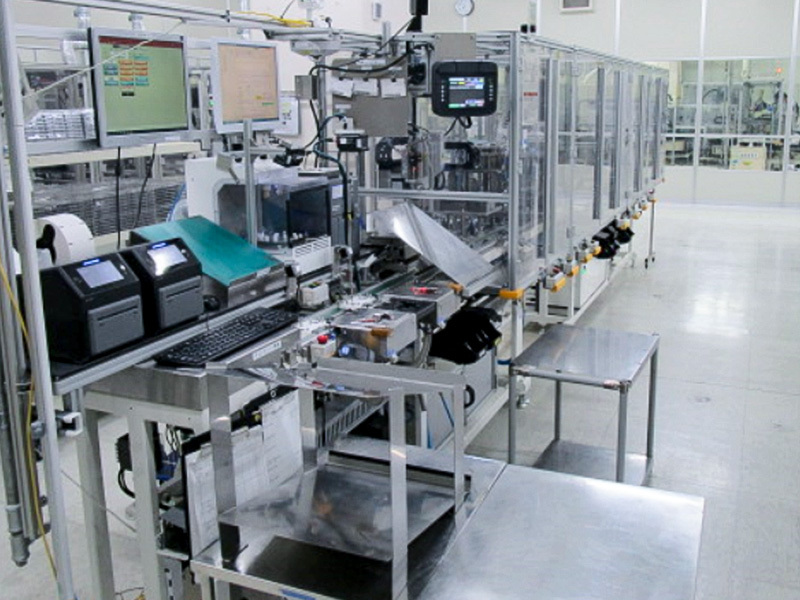
Implementation lines (left) , and assembly lines
The introduction of AI technologies has drastically reduced the labor required to analyze the current situation, which traditionally depended on people’s skill. Using the time saved, people can now dedicate themselves to eliminating waste visualized by AI. In the nine months since the introduction of AI technology last September, productivity at the manufacturing site has doubled, a significant improvement.
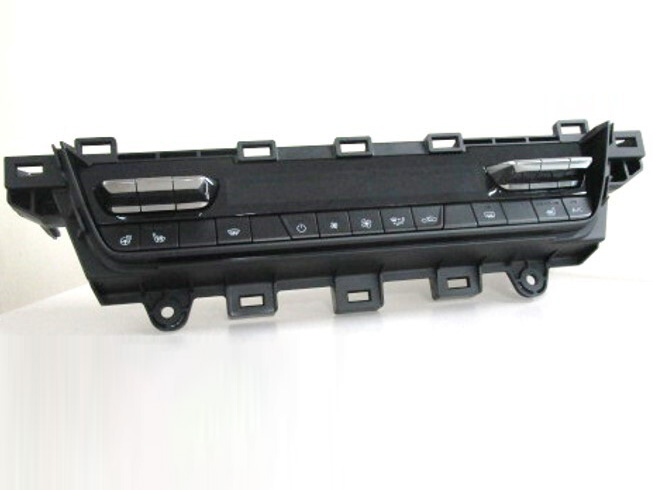

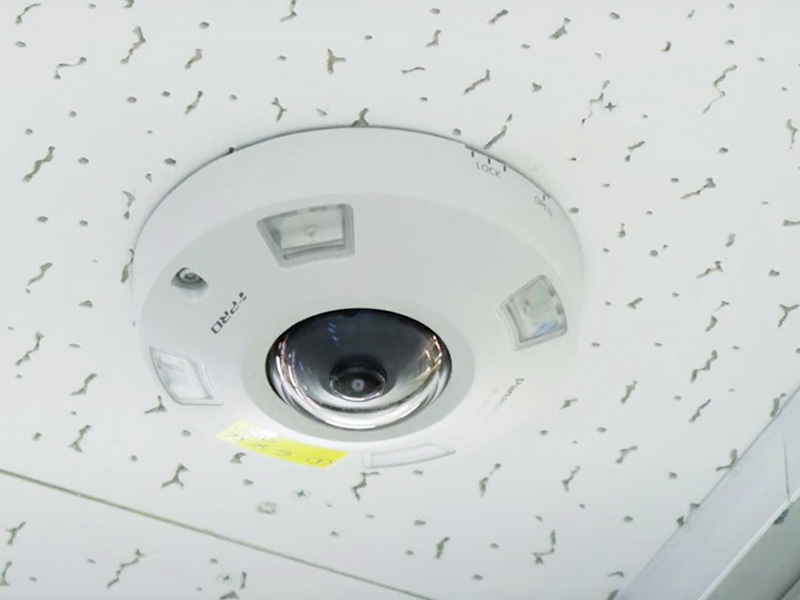
<Interview with a key person on site: Mr. Takeuchi>
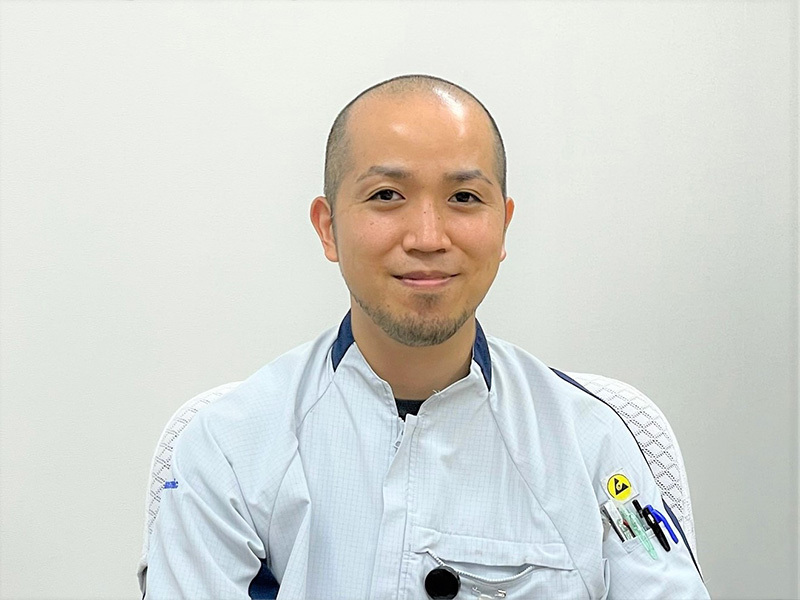
Q: Has the worksite changed?
Mr. Takeuchi: I feel that the thinking process of Gemba Innovation has been properly accepted, and everyone’s awareness has changed. For example, we ask workers to write comments on work loss and other information on the digital production control board, and everyone has started to write more and more information.
The digital production control board is a system that lists the production plan for each item and allows the production status to be monitored in real time. By digitalizing the previously analog system, members can now check the status from anywhere, at any time. When a worker posts a problem on the production control board, other members will help them. When issues are addressed, improvements are made, and as a result, the work at the site becomes easier. This positive cycle has accelerated rapidly, and productivity at the worksite has seen major improvements.
Q: So the effect of digitalization was significant?
Mr. Takeuchi: Actually, I was personally skeptical about digitalization. This is because you can’t really improve the worksite unless you have acquired the improvement thinking process in the first place. However, the fusion of the improvement thinking process and digitalization has changed everything, increasing productivity significantly, and the time that has been freed-up can be used for other more creative activities.
Q: What are your goals for the future?
If the work at the manufacturing site becomes easier, product costs will improve, cash will increase, and business will improve. Gemba Innovation and on-site improvement is a method that supports business. I believe that better manufacturing is our company’s true competitive edge. We will continue to make constant improvements based on the words of Panasonic founder, Konosuke Matsushita: “employees as entrepreneurs.”
<Interview with the manager: Mr. Nakazono, Head of Electromechanical Devices BU>
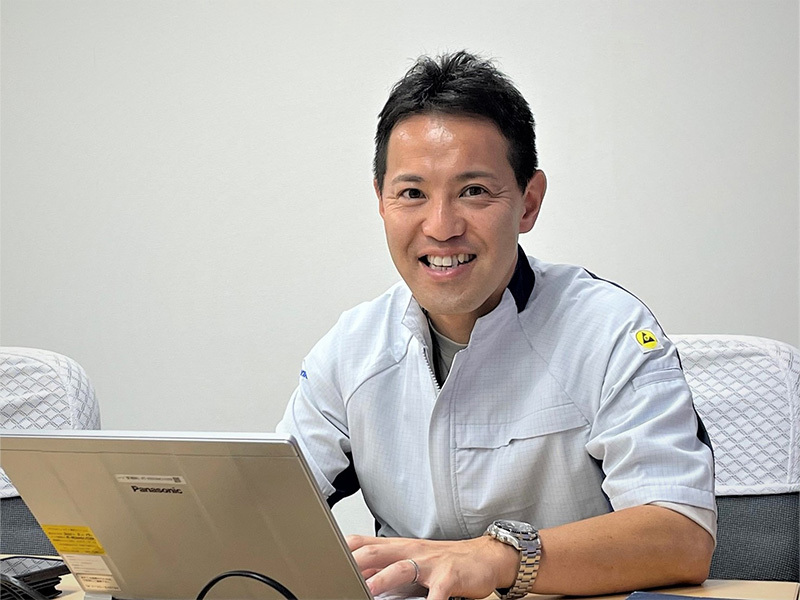
Q: The workplace seems to have changed dramatically thanks to the capabilities of digital technology.
Mr. Nakazono: The influence has spread not only to the Manufacturing Department, but also to the entire BU, including the back-office and the Procurement Department, and we have been able to get many people involved in Gemba Innovation activities. We feel that the visualization of results has increased our motivation, and applying digital technology has become easier. Above all, the quality and speed of kaizen has improved, as employees have more time to think and can grasp broader perspectives.
Q: What kind of organization do you want the Electromechanical Devices BU to grow into?
I would like to play a role in the growth of Panasonic Group as a top runner in manufacturing innovation. Business for car manufacturers has a relatively long product life cycle, and improvements easily take root in the workplace. I would like to take advantage of this characteristic to take on the challenge of next-generation manufacturing. By adding digital tools to the manufacturing capabilities we have refined, we will further advance our adaptability and become a stronger company.